Our News
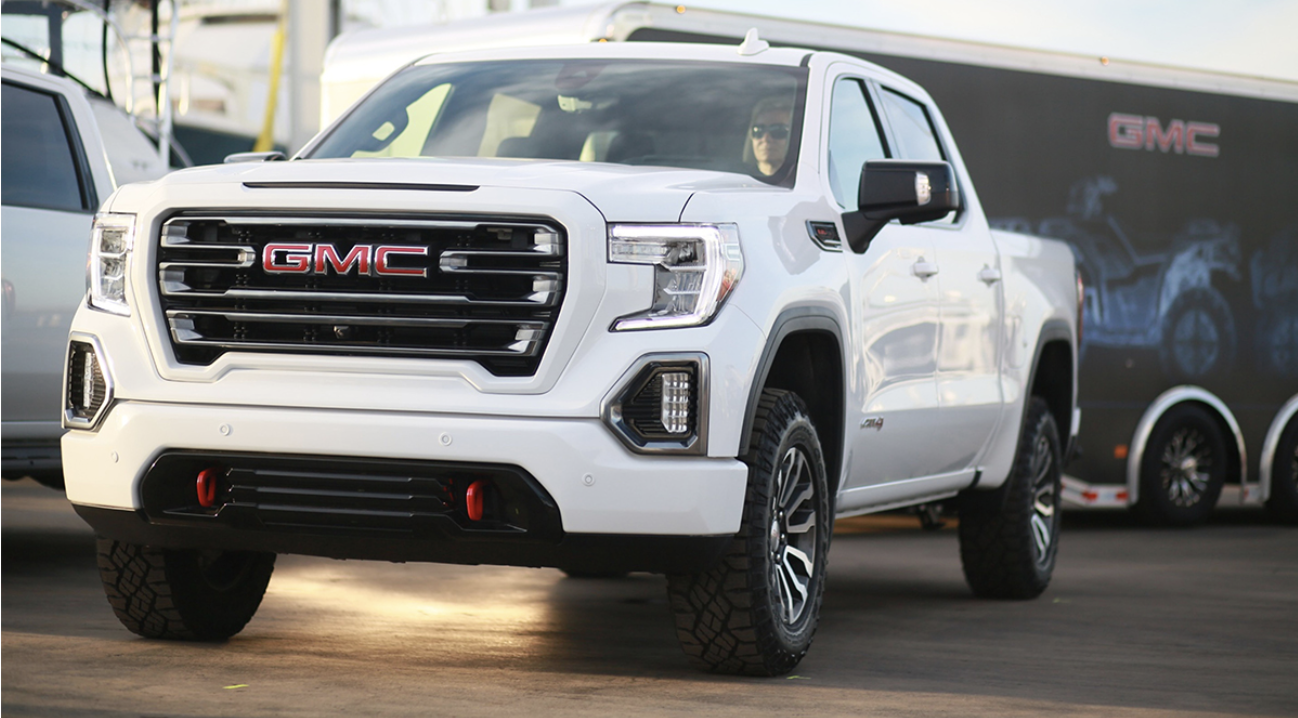
Self-driving technology is coming to a pickup truck near you. GMC says it will offer its hands-free driver-assistance feature Super Cruise on its Sierra pickup sometime in 2022. While the Sierra will not be the first GMC product to option the award-winning technology — that honor will go to the Hummer EV in 2021 — the Sierra is by far the highest-volume GM product to receive the technology thus far. The Sierra joins a rush of semi-autonomous trucks coming to market over the next two years, including the Ford F-150, Rivian R1T and Tesla Cybertruck. Ford’s Active Drive Assist — a hands-free system similar to Super Cruise — is available for GMorder on the all-new 2021 Ford F-150, which has been the best-selling truck in America. The F-150 is due to arrive on dealer lots in the third quarter of next year. Super Cruise will debut on Sierra’s premium Denali trim, and will function while towing. “We’re putting Super Cruise on a Sierra. [It’s] the world’s first true, hands-free driver-assistance tech available pretty much across the United States,” GMC marketing executive Phil Brook said. So it won’t “just be in the big cities [but] in every state because … Sierra, it’s such a popular vehicle.”“We’re putting Super Cruise on a Sierra. [It’s] the world’s first true, hands-free driver-assistance tech available pretty much across the United States,” GMC marketing executive Phil Brook said. So it won’t “just be in the big cities [but] in every state because … Sierra, it’s such a popular vehicle.” Super Cruise debuted in the low-volume, now-discontinued Cadillac CT6 in 2016 and is slowly being expanded to the full Cadillac lineup. But the entire Cadillac brand typically sells just 150,000 units in a typical year, whereas Sierra alone typically sells 220,000. The low-volume, battery-powered Chevrolet Bolt EUV (an SUV companion to the Bolt EV hatchback) will also get Super Cruise when it goes into production next year. Super Cruise and Tesla’s hands-free Autopilot are the leading semi-autonomous systems on the market. But unlike Autopilot, Super Cruise only works on divided highways, where GM believes it is safest and most practical. Ford will debut a similar system next year on its Ford F-150 and electric Mustang Mach E. GM’s Super Cruise (and Ford’s Active Drive Assist) use a camera and infrared lights to ensure the driver is paying attention to the road. Along with GPS mapping and radar sensors, this allows vehicles to drive hands-free on divided highways across North America. While the Tesla Autopilot system prompts drivers every 30 seconds or so to keep their hands on the wheel, the Super Cruise system allows the driver to relax hands-free. Super Cruise only intervenes with escalating alerts if it detects the driver’s eyes aren’t looking ahead and paying attention to the road. Autopilot debuted on Tesla’s Model S sedan in 2014 and has grown in ambition with over-the-air updates. It pioneered automatic lane-change capability in 2018 and is now capable of stopping for traffic lights and negotiating stop signs and pedestrians. GM has charted a more conservative path by limiting the feature to highways, and will introduce automatic lane-change next year. Its conservative approach earned it the prize for best driver-assistance system this year from Consumer Reports. Available on select, higher-trim Cadillac models beginning next year, the Super Cruise option is about $2,500, but should cost less on the high-profit Sierra. On the F-150 and Mach E, expect Ford’s system to cost about $1,600. The brands will charge monthly subscription costs on top of that. Industry analysts say that the Super Cruise take-rate on the Cadillac CT6 was about 30%. If that number holds on the Sierra, it should put nearly 70,000 vehicles on the road a year beginning in 2022 with hands-free capability.
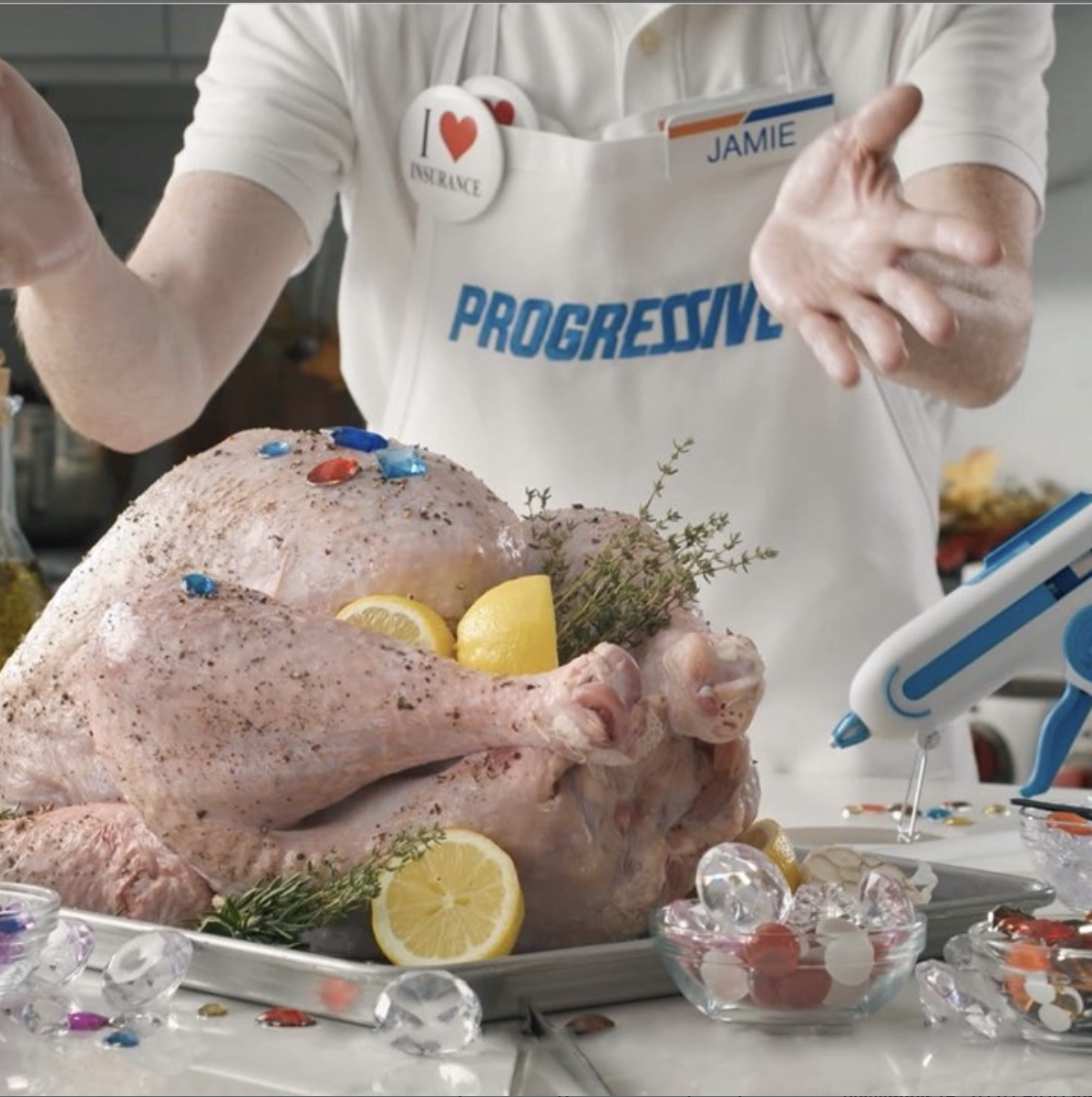
If you're anything like me you'll be amused by this weird news you can use, so let's talk turkey. According to Butterball 4/5s of Americans celebrate Thanksgiving. And out of those 4 at least one family completly demolishes Americas favorite main event THE TURKEY! I guess turkey isn't the easiest thing to make but hey everyone isn't a chef. If you are still worried about a Thanksgiving Day fowl fail, why not insure your turkey with Progressive? YES INSURE! Whole Foods Market and Progressive Insurance have a new way to insure your Thanksgiving meal against those dreaded holiday accidents. To qualify for "coverage," purchase a Whole Foods Market brand turkey today. Yes I know you're wondering why did I decided to write this blog on the last day. I actually just randomly came cross the article.But if you burn, undercook, overcook or commit another turkey fail between Thanksgiving and Black Friday, visit www.turkeyprotectionplan.com to submit a claim. Now the more and more that I think about it this may not be too bad of a idea. Millions of Americans are expected to have scaled-down celebrations amid the coronavirus pandemic, heeding official warnings against travel and large indoor gatherings. The first 1,000 eligible claims get a $35 Whole Foods gift card! "As we anticipate more smaller Thanksgiving gatherings and first-time cooks tackling turkey preparation this year, the Thanksgiving Turkey Protection Plan allows customers the freedom of culinary exploration, knowing all is not lost should their cooking go astray," Theo Weening, Whole Foods vice president of meat and poultry, said in a news release. I mean hey, turkeys are pretty expensive now a days might as well get your money worth. 🤗 https://www.usatoday.com/story/money/food/2020/11/10/thanksgiving-turkey-whole-foods-progressive-insurance-protection-plan/6239911002/
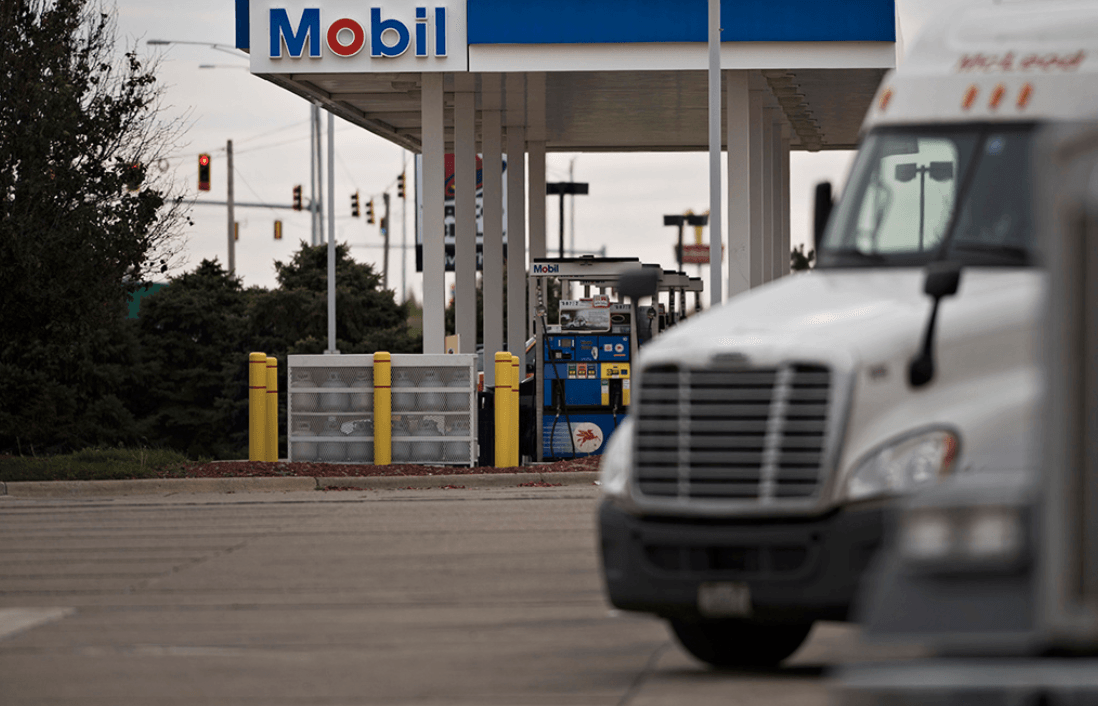
The nationwide average price of diesel fuel fell by 1 cent, the fourth consecutive weekly decline, according to the U.S. Energy Information Administration’s report released Sept. 28. Meanwhile, in a truly unusual report, the national average price of a gallon of gasoline increased by one-tenth of a cent to $2.169, despite the price falling in nine of 10 regions. The one region that saw an increase, the Midwest at 2.5 cents a gallon, was enough to swing the overall national price into upward territory. A gallon of trucking’s main fuel stands at $2.394 a gallon. Diesel costs 67.2 cents a gallon less than it did a year ago. Every region across the country saw prices drop. California experienced the most significant fall, 2.1 cents to $2.541. The state still has the most expensive diesel at $3.236 a gallon. The Gulf Coast had the smallest drop, 0.3 cent, settling at a nation-low $2.154 a gallon. Three regions saw decreases of 1.3 cents; the East Coast stands at $2.473 a gallon, the Midwest at $2.269 and the West Coast at $2.928 a gallon. The Rocky Mountains saw a 1.2 cent-decline to $2.336 a gallon.
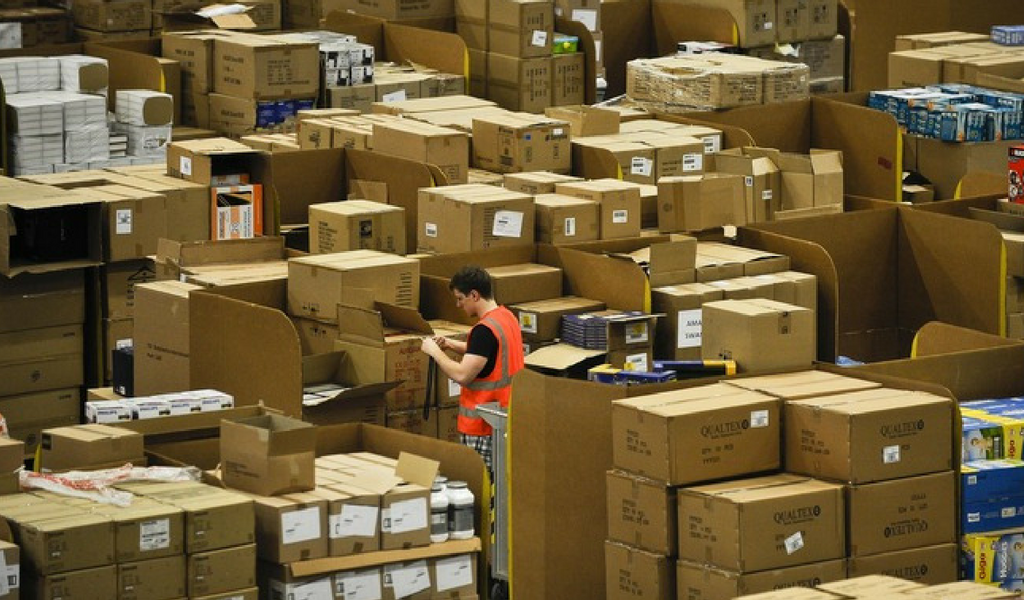
Ecommerce behemoth Amazon’s ever shorter delivery times have created lofty expectations among customers of supply chain and logistics businesses. Deliveries that span days are now viewed with some degree of derision and disbelief. There’s pressure to deliver quicker without any significant change in delivery prices. Delays aren’t tolerated. That’s why supply chain and logistics enterprises must have a plan to mitigate against any last-minute issues that could constrain their ability to get a delivery to its destination. There’s perhaps been no better time to plan for such disruptions than now. The COVID-19 pandemic may be a health issue but it has had a profound impact on global supply chains. When the novel coronavirus was at its peak, factories were closed all over the world. This unexpected shutdown affected manufacturing and shipments across the globe. When last-minute issues such as these come up, certain things will be outside your control. However, there are actions you can take that can help mitigate the negative impact. Here’s a look at last minute issues and how you can sort them out in-house. 1. Disruption to Transportation Natural disasters can occur with no warning. Earthquakes can damage roads, floods render driving impossible or volcanic eruptions ground flights. Such disruption to the means of transportation you depend on for your delivery would make it harder to get your package to the customer in time. Waiting out the disruption until the transportation is restored would be one way. A better solution would be to have an alternative means you would deploy if the primary one is rendered temporarily unusable. If your shipments are conveyed by air, would it be feasible to get them to their destination via road or rail? For relatively near destinations, it may be possible to do this and still get the package to its destination in time. For further off locations and if you are devoid of options, you could advise the customer that their shipment will be delayed due to circumstances beyond your control. If you already have intermodal transportation built into your delivery, you’ll have a considerable advantage in switching from one means of transportation to another. 2. Missing Carrier Cutoff If you are using a shipping carrier, something could happen that makes it impossible for your shipment to make the cutoff for next-day delivery, 2-day delivery or other delivery target. When that happens, your options would depend on the value of the order and your judgment of the urgency. For example, if you have a delivery where your profit margin is in the tens or hundreds of thousands of dollars, booking a private jet could be well worth the extra expense. You could even do the delivery via a commercial plane, a cheaper option than a private jet. A more long-term solution to mitigating carrier cutoff is to establish your facility or take up warehouse space close to the carrier’s collection and distribution hub. With that, you’d require less time to get your items to the carrier which gives you more time to play with. 3. Systems Failure Various technologies have made the logistics landscape much more transparent and quicker than it’s ever been. Employees and customers can log in to dispatch and track orders. Supply chain businesses and delivery services can stay on top of their capacity and customer locations. But technology can and does fail. And such failure could happen when the system is most needed. Information technology brings convenience and scale but a system failure shouldn’t bring your business to a complete halt. At the minimum, you must have redundancy in place that allows you to launch a backup system. That way, you can continue your work with minimal interruption to the customer experience. Second, you must have a manual workaround that would allow the delivery process to proceed somewhat while your systems are down. 4. Sudden Unavailability of Critical Staff Modern-day delivery may rely heavily on technology but it’s the staff along the entire delivery chain that actually make things happen. If a sizable number of your most critical employees are suddenly unavailable, that could make it harder for you to fulfill deliveries in time. In the context of the COVID-19 pandemic, think about employees who may have been forced to self-isolate following suspected exposure to the virus. You need a robust mechanism for ensuring any staffing gaps are filled quickly and by competent persons. Pairing each member of staff with the right backup person is something you should do beforehand. Leverage the power of staff scheduling software to, for example, fill in shifts based on drivers’ availability, skills, experience or location. Quickly match employees to emerging gaps for a smooth transition when any critical staff is suddenly absent. Wrapping Up the Issues in the Delivery Process Your ability to respond to last-minute issues in your delivery process can only be as good as your planning for it in advance. The better prepared you are for any eventuality, the less you’ll need to take expensive extreme measures. Overall, always leave time and financial room to accommodate any last-minute events that could inhibit delivery. With these healthy margins of error, you retain some flexibility to ensure the shipment gets to the recipient on time.
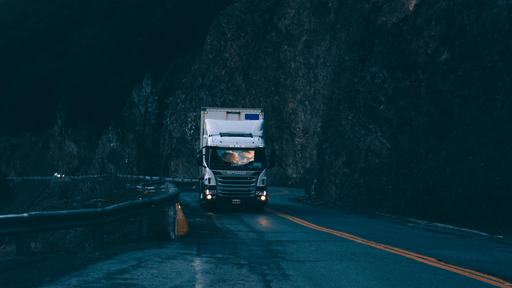
The novel coronavirus, also known as COVID-19, has contributed to what might be described as the biggest supply chain shipping disruption of the century. According to the CDC, the total number of cases in the U.S. had jumped to 2,438.887 as of June 23, 2020. More than 35,000 new coronavirus cases were identified across the United States on Tuesday, according to a New York Times database, the highest single-day total since late April and the third-highest total of any day of the pandemic. As the United States continues to reopen its economy, case numbers are rising in more than 20 states, mostly in the South and West. Florida on Wednesday reported a new daily high of 5,508 cases. Texas reported more than 5,000 cases on Tuesday, its largest single-day total yet. Arizona added more than 3,600 cases, also a record. And in Washington State, where case numbers are again trending upward, the governor said residents would have to start wearing masks in public. In March, The President invoked the Defense Production Act, DPA or the Act, which as a precautionary measure, would grant added powers to the government to impact manufacturing and shipping. As a result, shippers need to understand a few things about the Act and what it means for the continuance of operations. What Is the Defense Production Act The Defense Production Act grants power to the U.S. president to force companies to produce goods for the U.S. during times of war or other crises, explains Tech Crunch. On the surface, the Act looks to force manufacturers to start producing materials needed to meet demand, such as hospital masks, other personal protective equipment (PPE), and ventilators. However, that is not the way the Act functions. Instead, it focuses on changing the way companies fulfill orders—putting the government at the highest authority and prioritizing needs for the government over others. For example, ventilator manufacturers could be required to produce more units for the government first before fulfilling orders for individual facilities. With that in mind, it is important to note that while the current administration has invoked the 20th-century law, it has not yet placed any known, public orders for items. In other words, the current state of the industry is operations as normal, unless otherwise specified by local or state governments that might limit operations. Businesses and those involved in “essential” supply chain operations, including grocers, pet stores, adult beverage sales, and financial institutions, can continue operating. The goal is to reduce panic and still maintain a degree of normalcy for the foreseeable future. Which Shippers Will Have Challenges in Meeting Requirements Under the DPA The requirements under the Act are simple; fulfill government orders first. Now, that might not be a problem for some shippers, but for those that have made the mistake of forgoing e-commerce fulfillment will pay the highest price. Without e-commerce, traditional, non-essential businesses will be faced with a complete halt of operations. Customers will go unserved, and the supply chain will take a major hit. Moreover, shippers with limited visibility into operations and the inability to prioritize orders across multi-site locations will have an additional problem with fulfilling orders—assuming they are placed by the federal government—in a timely manner and keeping up with consumer demand. As explained by Warren Shoulbery of Forbes: “That irrefutable outcome of the pandemic will make retailers that have never truly developed e-commerce capabilities—or, worse, walked away from the channel—do a 180-degree turn and put a massive push behind getting their online operations into competitive shape. Although most national retailers have been in the e-commerce game for decades, it’s fair to say that few of them have their acts totally together. While Walmart and Target on the discount side, Macy’s in department stores and specialty retailers like Best Buy, Williams Sonoma, RH and the Gap brands have healthy online businesses, other sectors are far behind in building their e-commerce sales. Amazon’s expanded business over the past few weeks is one more piece of proof.” How to Continue Operating Throughout Shipping Disruption Today’s businesses can quickly mobilize and enact crisis-management mechanisms. According to McKinsey & Company, companies must take these steps now to prepare for a possible future under the Defense Production Act, as well as changes to fundamental fulfillment and shipping: Create transparency on multi-tier supply chains. Estimate available inventory. Assess realistic demand. Optimize production and distribution. Identify and secure more capacity. Manage working capital and cash to reduce financial impact. Use data to make informed decisions. Increase inventory management capabilities through optimized, self-guided ordering systems. Connect with customers to create a level of trust beyond the traditional standard. Diversify carrier relationships to secure more capacity as trucking takes its place in this shipping disruption. Increase available supplier relationships to avoid out-of-stock problems amid COVID-19 panic buying and government orders. The DPA Isn’t Going to Change Much About How You Resell Products Right Now There is good news. The president has yet to place orders or directives for agencies to order additional items under the Act. So, the time being remains business at the pace of fulfillment based on in-store demand for essential businesses and those that fall into similar categories. However, this current situation is an opportunity to learn an invaluable lesson; the next supply chain shipping disruption will come. Those that prepare now will be in the best position to avoid failures in the future.